Vision-Guided Robots and AI Drive Frozen Food Packaging Improvements
A prominent frozen foods company that produces 8% and 15% of all frozen peas, corn, and diced carrots sold in the United States recently ran into issues with an automated pick-and-place system. Fortunately for the company and for all frozen vegetable consumers, Oxipital AI’s AI-enabled vision system helped solve the issue. Read full case study…
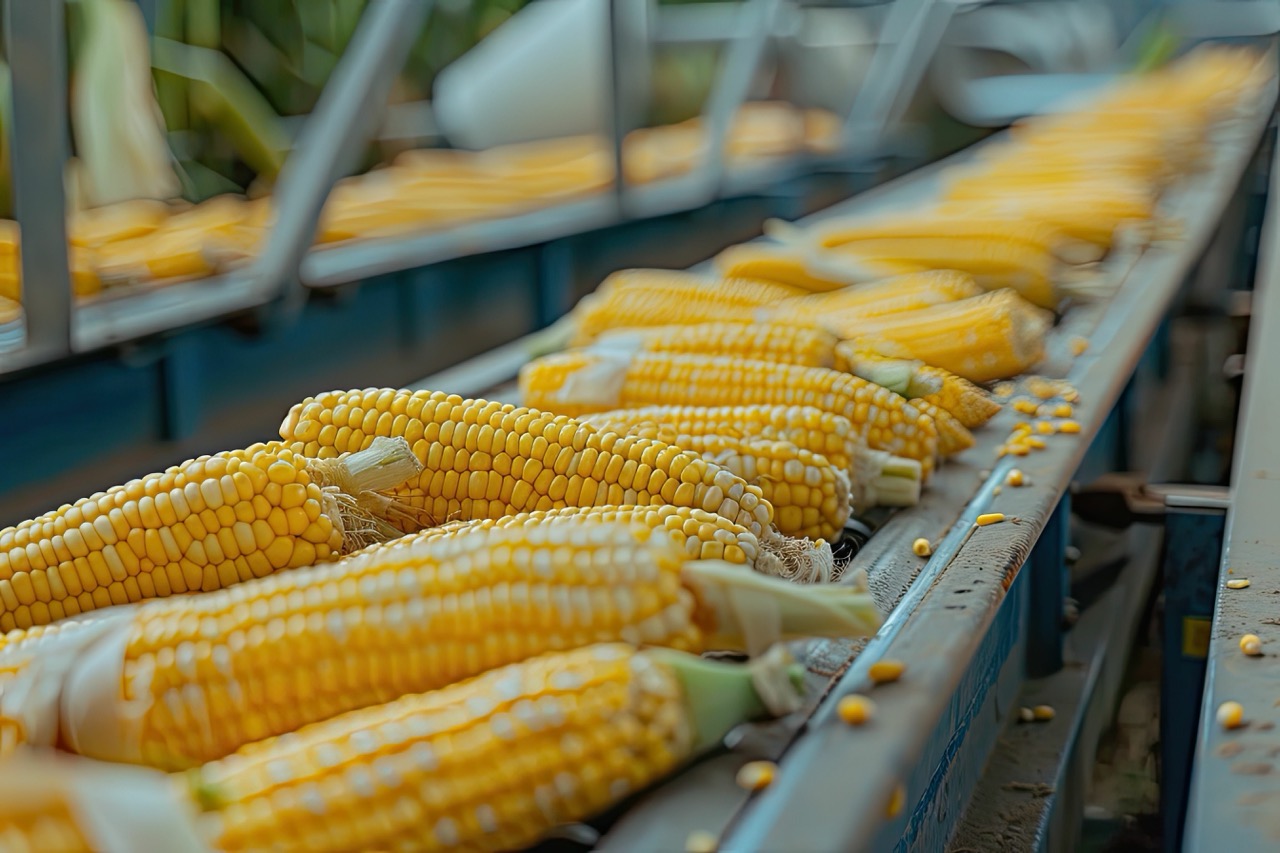
Cutting-edge software and vision system boost throughput and slash costs for food packaging company
Well-engineered vision systems paired with modern robotics can revolutionize produce sorting and packaging. Automated pick-and-place operations can provide far superior speed and accuracy compared to human hands. An improperly designed vision or automation system, on the other hand, can create waste and cause damage to robots.
A prominent frozen foods company that produces 8% and 15% of all frozen peas, corn, and diced carrots sold in the United States recently ran into issues with an automated pick-and-place system. Fortunately for the company and for all frozen vegetable consumers, Oxipital AI’s AI-enabled vision system helped solve the issue.
The Challenge
Initial System: Vision Flaws Emerge
The company deploys vision-guided robotics to assist in corn sorting and processing operations. Trucks dump loads of freshly picked sweet corn onto shaker tables, which feed the corn into de-husking machines. The de-husked corn falls onto another set of shaker tables and then onto one of six conveyor lines, with two ABB FlexPicker robots equipped with finger grippers stationed on each line.
The vision system integrator engineered the initial solution to capture images of corn on the conveyors and translate the data into pick instructions for the robots, which are tasked with picking the corn and placing it onto a lug conveyor for delivery to a machine that cuts either end of the cob. The resulting center cob pieces then drop from the lug conveyor into an individual quick freezing (IQF) process before packaging for shipment.
Project Overview
Increased Efficiency & Productivity
Oxipital AI’s vision system boosted pick rates by 27%, enabling thousands more picks per day and eliminating manual bottlenecks.
Reduced Costs & Waste
With over $300,000 in projected savings over five years, the AI-powered system reduced missed picks, minimized product waste, and lowered long-term maintenance costs.
Scalable & Future-Proof Automation
The AI-enabled solution provides real-time precision and adaptability, allowing seamless expansion to other product types and automated quality inspection for better yield tracking.
Optimizing Vision Systems for Accurate Robotic Picking
The cameras were placed too far upstream from the robots, which does not allow for tracking and adjusting for unexpected motion in the pick area. If a cob changed position on the conveyor between when its image was taken and when it arrived at the pick area, for example, the positional data no longer applied. The vision software also did not register whether the cob lay parallel or perpendicular to the conveyor, but the robots’ positioning assumed that the corn was parallel to the belt. These positioning issues resulted in missed picks.
In the best-case scenario, corn is simply not picked up by the gripper. A bad but not catastrophic result was an improper grip on the product, leading to the robot throwing the corn at the wrong angle, so it missed the lug conveyor and fell to the ground as waste. In the worst-case scenario, the grippers smashed straight through the corn, again ruining the produce and sometimes destroying the robot gripper itself. In these scenarios, production on the affected line halted entirely while engineers made repairs.
The vision system integrator had targeted 60 picks per minute per robot with the initial design of the system. Upon deployment, however, the system struggled to make 40 picks per minute and unfortunately, testing prior to operation hadn’t generated enough picks to demonstrate the issues that would later emerge.
OUR SOLUTION
Oxipital AI System: 27% Pick Rate Boost
Oxipital AI had an existing relationship with the company and considerable experience serving the food processing industry, specializing in AI-enabled vision systems with IP69K-rated hardware. Mike Welborn, director of business development at Oxipital, asked if his engineers could visit the processing plant and investigate the problem. “They’ve had this equipment in their facility for a couple of years, and it started causing problems from a yield perspective, a quality perspective, and a cost perspective. They weren’t realizing the return on investment they once thought,” Welborn says.
Alex Neufeld, applications engineering manager at Oxipital AI and his engineering team started with a single robot cell. They installed a vision system directly into the robot workspace in the pick area to generate positional data in real-time. The system uses 3D data and provides pose estimation data for all picks, which ensures that the gripper will align with the corn and result in missed picks and lost productivity. The AI-enabled vision software leveraged a pre-trained image model for corn and interfaced directly with the ABB robot’s PickMaster line tracking program.
It took only two weeks to deploy a new system on that first robot cell. During the first week, the team rewired the cell and connected new cameras and supporting hardware. It took two more days to tune the system. It ran so smoothly afterward that the team spent the remaining three days strictly comparing performance data between the cell running Oxipital AI’s vision solution and two cells running the old system.
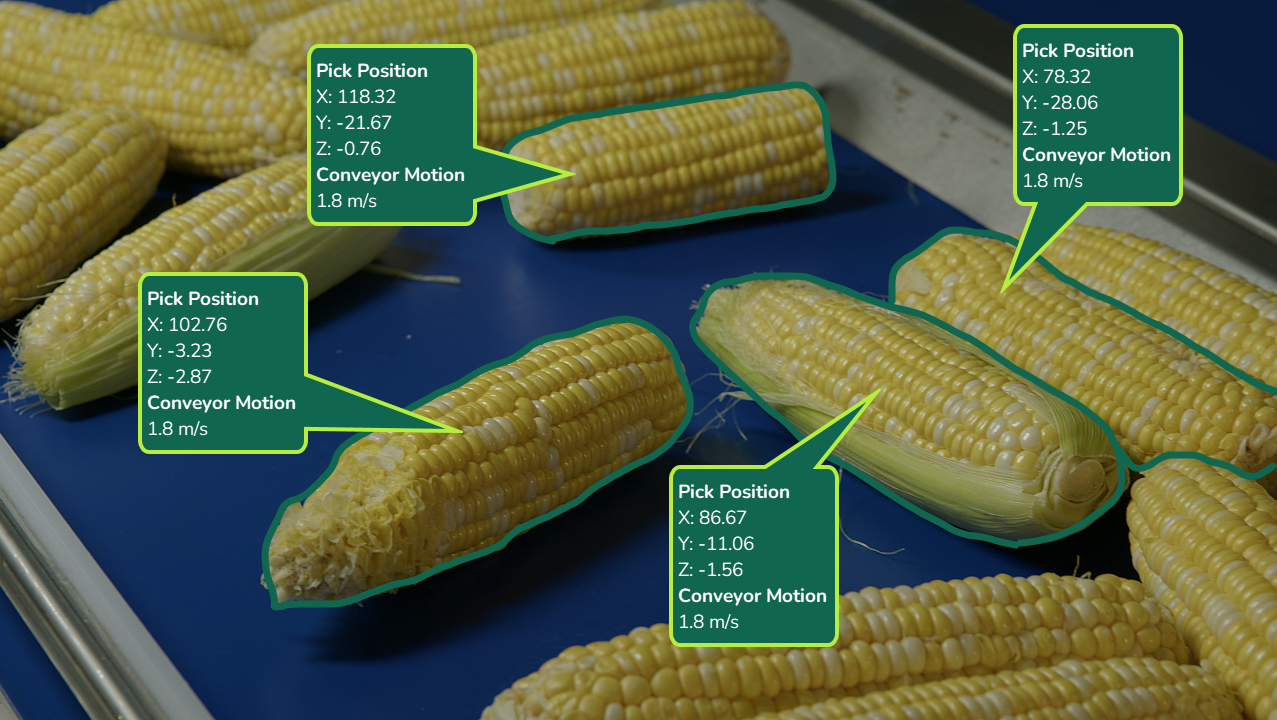
“We did about 5,000 more picks than one of the [non-AI] cells and did 7,000 more picks than another one of the cells. That’s 20% higher than one of the systems and 27% higher than the other system. Everybody who walked by would look at the new system and comment on how much more effective it is than the previous one,” says Neufeld.
Oxipital AI then completed the entire system, which runs on an industrial PC with an NVIDIA GPU for fast inference at the edge. “With these pretrained object models, we’re doing all the legwork, all this programming work, on the front end. You’re essentially getting a no-code vision system with a very user-friendly interface,” says Welborn.
In addition to solving throughput issues, the Oxipital AI system also stands to drastically reduce the company’s long-term maintenance costs for the robots. After four weeks of production, the robots on the Oxipital AI line required only a single finger grip replacement. While the corn production season ended shortly after the company modified the line with Oxipital AI’s vision system, thanks to the use of pre-trained image models, the system could easily be modified to work with other types of produce simply by uploading new image models.
The Results
Versatile Vision, Easy Expansion
Oxipital AI’s vision technology can provide more than pick accuracy and efficacy improvements. The system can also perform inspection applications, such as determining whether any of the corn in the picking area has remaining husks, missing kernels, or rot.
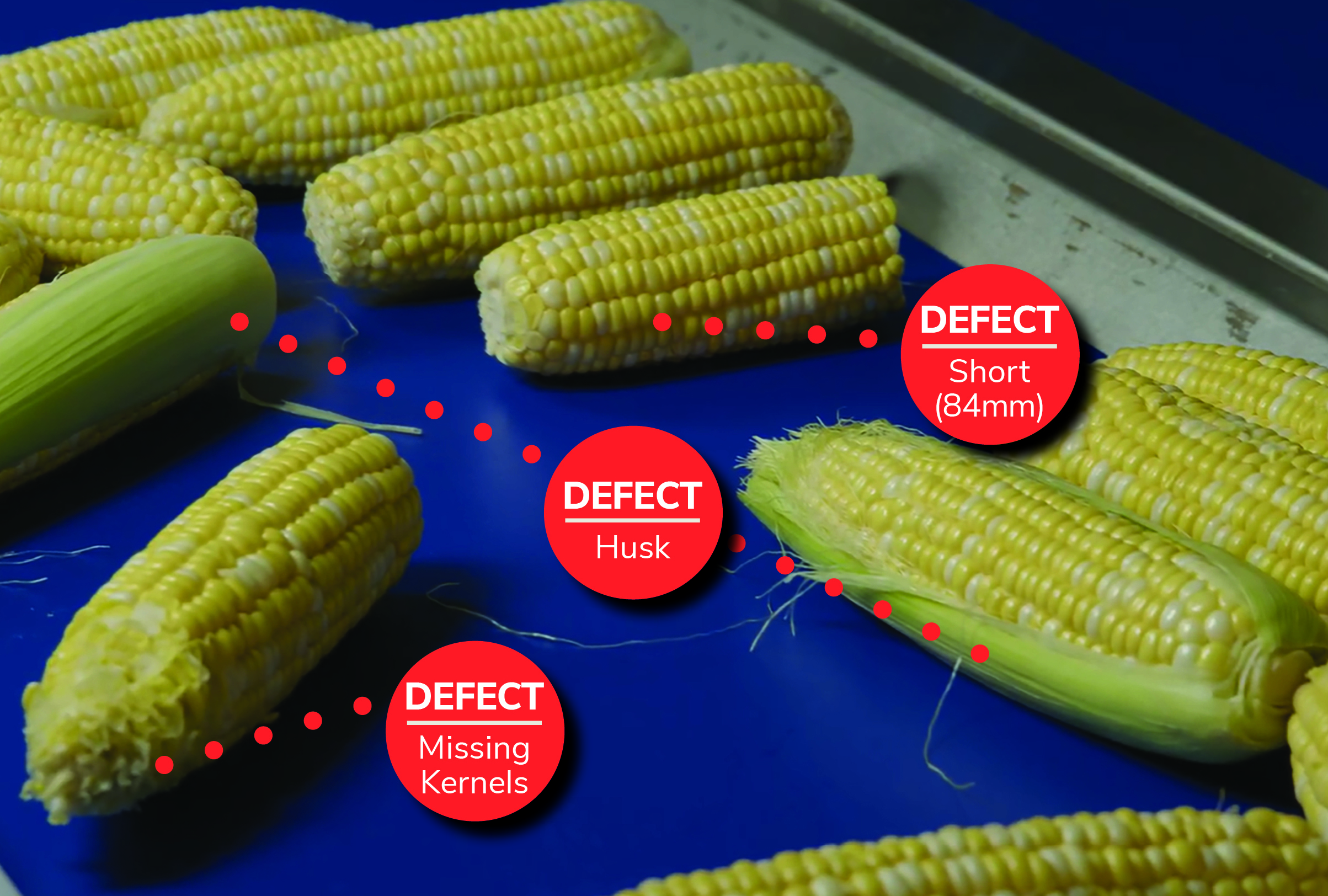
“It’s a simple thing for us to turn on the inspection piece, so food processing companies can get an idea of what type of defects they’re seeing, what their yield percentages are, and what their throughput is. . . . They’re able to capture and view all that data into a dashboard for reference, setting themselves up to gain more insights into their production,”
Mike Welborn, Director of Business Development, Oxipital AI
Contact us to schedule a demo or to see how AI-enabled pick-and-place and inspection technology can quickly and easily transform your plant operations.