Frozen Pizza Manufacturer Rolling in the Dough with the Help of AI
For one frozen pizza manufacturer, Oxipital AI’s technology means saving more than $5,000 a month while providing customers a consistent, high-quality product while delivering tangible economic benefits and operational improvements. Read full case study…
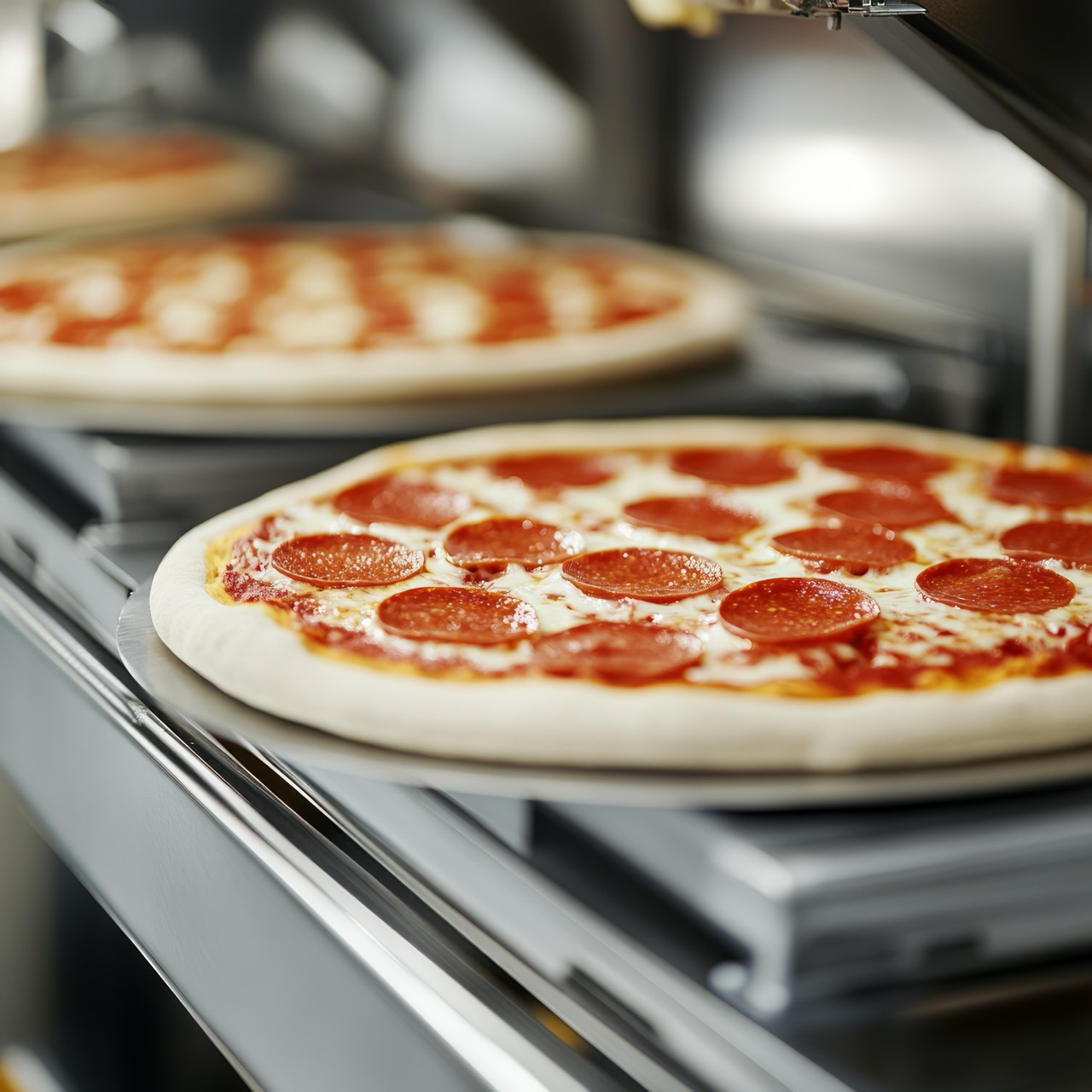
The Challenge
Manual Process Impacts Quality
A leading U.S. frozen pizza manufacturer has launched an innovative initiative to improve production efficiency and product quality. The manual method of adding pizza toppings frequently resulted in inaccuracies that affected the overall quality of the pizzas. Customers requested improvements and stricter quality control measures to rectify the problem. In response to this demand, the manufacturer sought out assistance from Oxipital AI to evaluate their OX1 Vision Solution, aimed at boosting quality and efficiency.
OUR SOLUTION
All-In-One OX2 Vision Solution
Following an evaluation, the pizza manufacturer decided to implement the OX1 Vision Solution as a pilot project in their operations. The system was installed in one day without disrupting the production line. Once installed at the end of the line, the system inspected individual pizzas and toppings through their plastic wrapping.
The OX1 is a powerful, easy-to-use inspection solution that provides high-speed, comprehensive visual inspection of variable objects in complex processing operations. With its IP69K rating and food-grade materials, the OX1 optimizes complex manufacturing processes in the harshest environments found in the food processing industry, surpassing existing vision-based inspection technologies. The OX1 can replace manual quality control tasks, performing high-reliability defect detection on 100% of items produced at full production rates.
Project Overview
Cost Savings
Over $300,000 in projected savings over five years by replacing manual quality control roles with the OX1 system.
Enhanced Product Consistency
Minimizes over-topping errors, ensuring higher quality and more consistent products.
Improved Efficiency
Automates inspections at full production speed, eliminating the bottleneck of manual quality control.
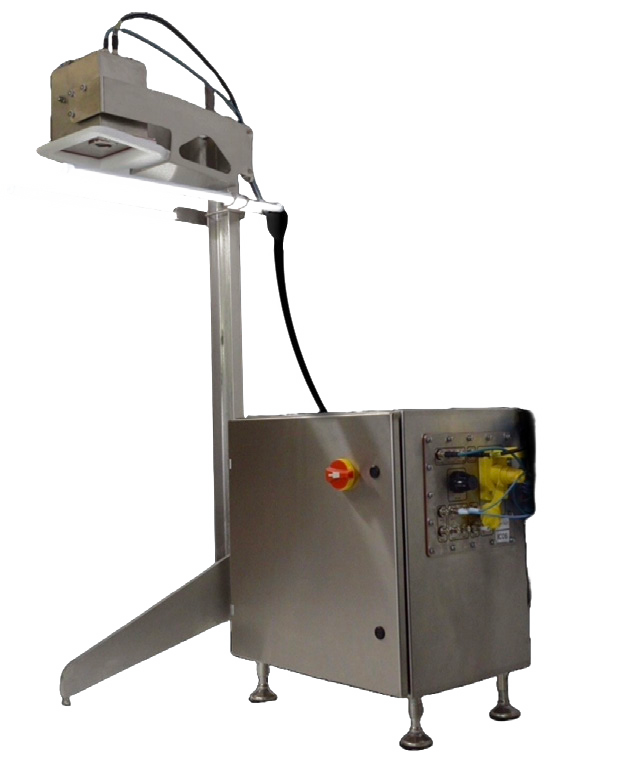
Deep Object Understanding Made Simple
Pre-trained object models from Oxipital AI enabled the customer to get up and running from day one without having to gather and label imagery. As with all OX1 customers, this pizza manufacturer used the no-code tools from Oxipital AI to digitally implement their quality guidelines on the system, keeping them in the driver’s seat of the application. The no-code tools enable them to flex with the needs of their customers to provide the highest quality product.
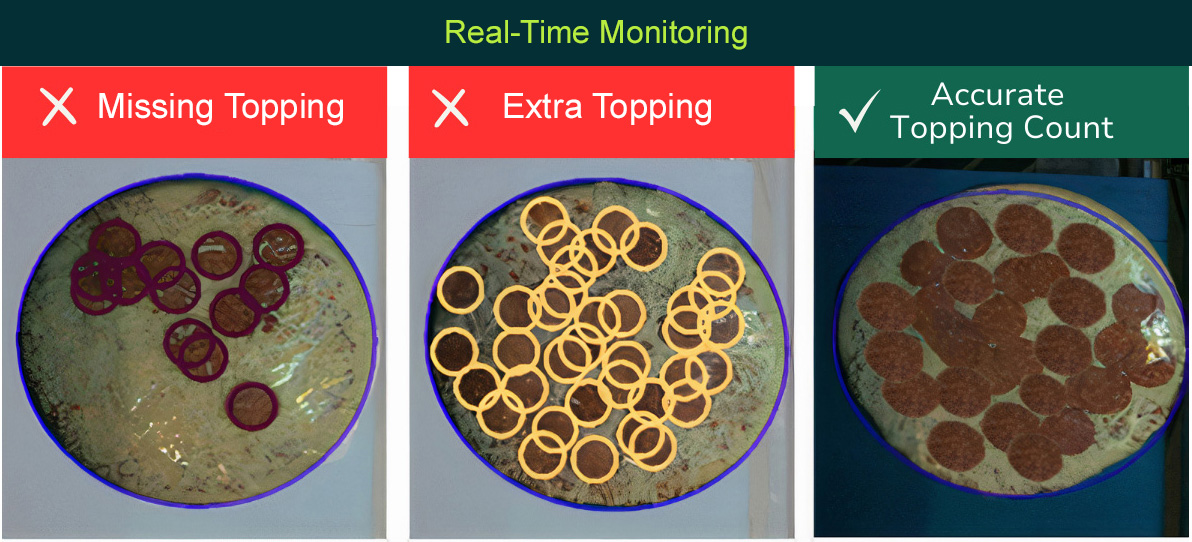
The Results
AI Results in Substantial Operational Benefits:
After weeks of use in operation, the customer was impressed by the ease of use, implementation, and results of the OX1 vision solution. Savings per operating line:
- Reduced Operating Costs: Projected savings of over $5,000 per month in operational expenses.
- Enhanced Product Consistency: Minimizes over-topping errors and enhances customer satisfaction.
- Improved Margins: Supports sustainable growth through cost efficiency and consistent quality.
Oxipital AI System: > $300,000 Savings in Five Years
The OX1 system has proven to be a game-changer for our client, delivering tangible economic benefits and operational improvements. Because of the OX1’s pilot success, the company has purchased additional systems for its manufacturing facility. Adopting this cutting-edge technology reinforces its commitment to quality, efficiency, and customer satisfaction.
By replacing two quality control full-time employee roles with a single OX1 system, our client projects five-year savings of over $300,000. The savings breakdown includes initial hardware costs, amortization, and ongoing dashboard access:
- Year 1 Savings: > $21,000
- Year 2 Savings: > $38,000
- Years 3-5 Savings (annually): > $83,000